Slate
Blackcurrant
Watermelon
Strawberry
Orange
Banana
Apple
Emerald
Chocolate
Marble
Slate
Blackcurrant
Watermelon
Strawberry
Orange
Banana
Apple
Emerald
Chocolate
Marble
Archived
This topic is now archived and is closed to further replies.
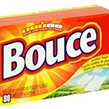
Fun with crossgrinding wheels
By
JR Boucicaut, in Ice Hockey Equipment