-
Content Count
27 -
Joined
-
Last visited
-
Days Won
1 -
Feedback
0%
ZamboniFever last won the day on December 7 2017
ZamboniFever had the most liked content!
Community Reputation
32 GoodAbout ZamboniFever
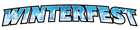
-
Rank
Sparx Hockey
Profile Information
-
Spambot control
765347789
-
Gender
Male
Recent Profile Visitors
-
Sparx Skate Sharpener - At home sharpener
ZamboniFever replied to tamtamg's topic in Ice Hockey Equipment
Hi @Healthyscratch Please send an email to help@sparxhockey.com and our customer support team will help you diagnose and resolve whatever issue you're having. I'll let them know you'll be reaching out so we get you squared away quickly. Regards, Russ Sparx Hockey -
Sparx Skate Sharpener - At home sharpener
ZamboniFever replied to tamtamg's topic in Ice Hockey Equipment
@IPv6Freely you're OK to finish off the old one that you have. The situation is that we no longer felt that heavy duty use of that ring COMBINED with not following the safety instructions in the Sparx Manual was an issue. Feel confident to finish off that ring but make sure to vacuum out your system and replace the dust filter as prescribed in the manual. https://cdn.shopify.com/s/files/1/0932/7770/files/11058C_V2_Users_Manual_Text.pdf?15916948694645149034 The routine maintenance defined in the manual also helps maintain peak machine performance and improves longevity of the system. -
Sparx Skate Sharpener - At home sharpener
ZamboniFever replied to tamtamg's topic in Ice Hockey Equipment
@hockeyrules we saw your message above. It sounds like you're using the our ES100 (consumer) machine. Based on your description, we think we know what's up with your machine and we'll take care of you to get things going right again. Can you please shoot a message over to help@sparxhockey.com with your info so we can get started? Regarding the Sparx Commercial Vacuum, we do hear sometimes from customers that they feel the vacuum isn't working well.... this is because of confusion on how the vacuum system works with the Sparx Commercial Sharpener. The vacuum's purpose in the system is to keep negative pressure (lower pressure than that of the room around the sharpener) so that any airborne particulate and dust is drawn into the sharpener enclosure (rather than wanting to go into the room). The vacuum does not try to suck up all of the dust that is trapped inside the enclosure. Capturing the dust inside the Sparx enclosure is the responsibility of the Sparx Dust Tray. Heavy particulate will drop into the tray and we recommend users to pull the vacuum hose from the port on the side of the PS100 sharpener once per day and vacuum out the heavy particulate from the tray. People often see this dust in the tray and think that the vacuum isn't sucking/pulling hard enough and that's not how the system is designed. I hope this helps. Lastly, on the number of cycles. Most of our commercial users that are using ES100s (our consumer machine) claim that they nominally run 5 cycles per skate for a good sharpening. We have commercial customers sharpening many thousands of pairs of skates per year using this technique. It helps sometimes to use the marker test on the heel and toe to confirm that the sharpening got the whole blade surface. I personally use this visual indicator since it only takes a second to mark the blade and it is proof positive that your sharpening was complete... well worth the extra couple seconds. You could even drop down to 4 cycles per skate with the marker test and then up a cycle if needed. The marker test also helps your customers out because you wouldn't be removing more steel than necessary on their blades. Lastly, our commercial customers using our PS100 systems have the cross grinding ring which does help out the situation of sharpening brand new or severely damaged steel. The cross grinding wheel removes steel much faster than the standard Sparx Grinding Ring. The cross grinding ring is no longer available for the ES100 system - much to the dismay of our ES100 customers (us too). This is because the swarf coming off the cross grinding wheel is too hot for onboard filter of the ES100 vacuum system. If you have any more questions, please shoot us a note over at help@sparxhockey.com. Our customer service and tech support teams are here to help. Cheers, Russ Founder/CEO Sparx Hockey -
Sparx Skate Sharpener - At home sharpener
ZamboniFever replied to tamtamg's topic in Ice Hockey Equipment
Leif, Please know that ProSharp's claim is not false. They just define things differently than we do. In our case we consider a sharpening, from a labeling standpoint, to be a sharpening that has 4 cycles on each skate. They describe a sharpening (indirectly... in their labeling) as 1 cycle on each skate (about 1000 cycles on a grinding wheel and about 500 sharpenings per wheel). Neither definition is wrong - they are just different. We chose 4 cycles in our definition because that amount of material removal is similar to what one would need to remove for a skate that was being sharpened on a pretty typical 4-8 hours of skating interval. Read below to see why this might not be the best way to describe a sharpening and why we are probably doing ourselves a disservice in our marketing because we say on our packaging 40 sharpenings per grinding ring. In reality, most Sparx users will get far more than 40 sharpenings per Grinding Ring. I personally get between 60 and 80 sharpenings on a Sparx Grinding Ring. Here's why... Once you have sharpened your skates AND if you have a sharpener easily accessible AND if that sharpener is super easy to use you WILL absolutely sharpen your skates a lot more (we hear this feedback from so many customers... skate sharpening frequency goes up because why would you ever chance it if it only takes a couple minutes to put on a fresh edge). I find I sharpen my skates every time (or every other time) that I skate. Because I am sharpening more frequently - I only need to make 2 cycles at most on each skate (less damage to the blades between sharpenings means less material removal needed). This means I am getting about 2X as many sharpenings (80 pair) out of a grinding ring vs the specification on the Grinding Ring box. I hope this helps clear things up... Thanks, Russ -
Sparx Skate Sharpener - At home sharpener
ZamboniFever replied to tamtamg's topic in Ice Hockey Equipment
I would like to help anyone considering these two products. Full disclaimer - I am the CEO of Sparx and a MSH member. Sparx and ProSharp Home are BOTH good products. That said, there is some misinformation in this thread that I hope I can clear up. You cannot directly compare Sparx to ProSharp on the amount of sharpenings per wheel that each company advertises the life of their wheels at. Reasons: 1. The two machines remove different amounts of material per pass. Sparx removes more material per pass than Home. 2. The two companies advertise different numbers of cycles required per sharpening. Sparx says you can sharpen 40 pair of skates with 4 cycles on each skate where ProSharp says they can sharpen skates with only 1 cycle per skate. These are not apples to apples numbers so you cannot compare the two numbers directly. How do you compare Sparx vs Home? Remove the same amount of material from a piece of skate steel, with both machines. Then compare the cost of the grinding wheel consumed by each machine to remove the same amount of material. We have done this head-to-head test of the two products and Sparx comes out cheaper than Home for the same amount of material removed. Please keep this in mind when considering the two products. When comparing Sparx to ProSharp Home you should consider the above and then also consider other details/differences between the two sharpeners. Each of the features below is exclusive to Sparx. 1. Sparx has a patented alignment system that eliminates the trial and error alignment steps that makes skate sharpening difficult. 2. Sparx has an on-board dust collection system which traps the metal dust generated by the sharpening process 3. Sparx has a safety glass front door which allows the user to safely watch the sharpening as it is happening. 4. Sparx offer the FIRE (flat bottom) profile which has been proven over the last few years to be one of the best flat bottom profiles out there. We have a youtube video explaining the FIRE profile if you want to learn more about it. 5. Sparx has electronic lock-out safety covers which cover the open slot around the skate reducing operator exposure to moving parts. Important if your sharpening is stored in a house where others may have access to the sharpener. 6. Sparx has numerous accessories like a loose blade holder which make sharpening Bauer Lightspeed Edge Removable steel, without the skate, really easy. Lastly, Sparx is used by thousands and thousands of customers all over North America and we also have hundreds of pro shops and teams using Sparx (see our "Find a Sparx Near Me" link below). We highly encourage hockey players everywhere to visit their LHS to get a Sparx Sharpening. If you don't see a Sparx Shop near you on the map please reach out to help@sparxhockey.com for help finding one as new shops are being added every day. https://www.sparxhockey.com/pages/skate-sharpening-near-me We also have a bunch of NHL teams and hockey skating coaches using Sparx now with their athletes. We have many videos on our YouTube channel where you can check out interviews with some high end Sparx users. Lastly, our roster of NHL player-owners is also growing every day... I hope this extra information helped. Thanks, Russ -
Sparx Skate Sharpener - At home sharpener
ZamboniFever replied to tamtamg's topic in Ice Hockey Equipment
Hi ryanmonty, Thanks for your notes/questions on our Warranty Policy. We just had a team meeting here at Sparx Hockey to review your concerns. Our policy had stated "Warranty is only valid in the country to which the Product was shipped at time of purchase." We have revised the policy to state "Warranty is only valid in the United States and Canada". We now honor our Warranty for Canadian customers regardless of the original shipping address of the sharpener purchase. You may have been living in the USA at the time of purchase and decided to move to Canada... the way things are going these days we need all the friends we can get in Canada ;) https://www.sparxhockey.com/pages/warranties Background - The limitation in the previous Warranty policy was a protection for us in cases where customers were located in regions where we currently don't have a service bureau (we will be expanding internationally very soon). Despite our current North American shipping restriction, Sparx sharpeners have already made their way to many countries in Europe, Asia, the Middle East, and Australia/NZ. For these locations it would be impractical to cover return shipping, which is included in our policy, on a warranty claim. I hope this clears things up and helps you with your decision. As always, thanks for your interest in Sparx Hockey products. Happy Holidays! Cheers, Russ CEO, Sparx Hockey -
Sparx Skate Sharpener - At home sharpener
ZamboniFever replied to tamtamg's topic in Ice Hockey Equipment
Thanks for the question @marka The Grinding Ring backorder situation was one that we anticipated but didn't catch quickly enough before the demand from our customers outstripped supply. This is an unfortunate, but not uncommon, problem for a rapidly growing company. I'm not using this as an excuse but letting you know what happened. I apologize for the inconvenience this is causing. The GREAT news is that we have doubled our production of Grinding Rings over the last month and are now working weekends at Sparx Hockey to build, pack, and ship product to our customers. Quality is also priority #1 for us. While we are growing quickly, rest assured that we are not cutting any corners on quality. We have the back order message on our website so that we are 100% transparent with our customers and also to set worst-case expectations. We strive with every order to beat the estimated time. In many cases these orders ship faster than the stated shipping delay. We fully anticipate to be flush with inventory of Grinding Rings and out of backorder in the next couple weeks. We will also be updating the message on the website soon since the delay to ship has been reduced from when we first posted this message. Many thanks to all of the MSH'ers who are Sparx Hockey customers. We appreciate your business and patience as we ramp up production. One silver lining from these short term shipping delays as we ramp up production is that this overwhelming demand for our product further solidifies us as a company - no worries about us being here for the long run. Sincerely, The Sparx Team -
Sparx Skate Sharpener - At home sharpener
ZamboniFever replied to tamtamg's topic in Ice Hockey Equipment
@Hills Good point. Let me explain. When an edge checker shows a deviation of 1 line from perfectly level (e.g. 1 line up on the right side of the edge checker), the opposite side of the edge checker should also show 1 line of deviation in other direction (e.g. 1 line down on the left side of the edge checker). This reading shows a combined 0.001" up on the right and a 0.001" down on the left or a total of 0.002" of height difference between the left edge and the right edge. To put this measurement magnitude into perspective, I just used a micrometer to measure the diameter of an eyelash. The micrometer reads 0.00325". The fact that the Sparx Edge Checker can measure your edges, in a repeatable fashion, to a fraction of the diameter of an eyelash is pretty impressive - speaking merely from an engineering perspective. Also, the Sparx Edge Checker and the other popular one on the market have the same measurement resolution. The lines may have slightly different spacing because the widths of the edge checkers are slightly different. Hopefully this makes sense. Cheers, Russ -
Sparx Skate Sharpener - At home sharpener
ZamboniFever replied to tamtamg's topic in Ice Hockey Equipment
One last comment... The rails that are on Sparx are not bent. We QC test all machines before they ship. If they were bent it would be evident in the test. Typically, the culprit here is the skate steel. A first step, if possible, is to sharpen the steel out of the skate holder. This usually allows the steel to be straightened by the Sparx clamp and the edges come out even. If that doesn't work, I then dive in checking to see if the edge checker readings are consistent when flipping the direction of the edge checker around while measuring. If they are inconsistent there is a high probability that the steel is tapered and throwing off the reading. Try sharpening another skate to see if you get the exact same results (preferably on a skate with at least 3 mm material removed from the blade - not brand new steel). Usually the results are different and many times this second skate will be dead even. Best approach once you arrive here is to trust that Sparx is sharpening your skate even... even if the edge checker is showing an inconsistent measurement (will still usually be within 0.001" of even). Hope this helps, Russ -
Sparx Skate Sharpener - At home sharpener
ZamboniFever replied to tamtamg's topic in Ice Hockey Equipment
Hello MSH'ers, This is Russ from Sparx. I'm hoping to be able to add some color around Skate Guru's review. This is a long reply so I had to clear out a couple hours on my schedule to write it which is my excuse for not replying sooner. Grab some popcorn and a comfy chair if you're going to read this one. Some background, we now have hundreds of shops using Sparx and our flagship install at New England Sports Center (NESC) in Marlbrough, MA has been using Sparx for 1.5 years now. They have sharpened 10's of thousands of pairs of skates on Sparx already. We work very closely with NESC and everything we learn there benefits all of our other customers. We also have an R&D lab in Boston where we run durability tests on all of our equipment. Sparx is built to last - both the consumer machine and the commercial machine. Now let's dive into each of the points Skate Guru (SG) makes in the hopes that I can provide a bit more detail. SG: Set up (9/10) - easy to set up right out of the box Sparx: If it's easy to set up right out of the box ... what would we need to do to earn a 10? The one thing we hear from nearly all of our customers is that they can go from receiving their Sparx sharpener to sharpening a pair of skates in 10-15 minutes without ever having sharpened a skate before in their life. I know I am biased but I might give Sparx a 10 on this one. SG: Adjustment (4/10): Problem is that the adjustment is in intervals and not graduated. So you are one click left or right and can not dial it in perfectly. Any experienced sharpener knows that CCM blades are wider than Bauer blades, Sparx: Adjustment intervals are graduated on purpose to make it clear to the user the exact amount they are adjusting. Each "click" translates to the grinding wheel moving in or out by 0.0015". This increment amount is more than enough resolution to position the grinding ring for even edges (note: moving the wheel in and out has a roughly 4:1 effect on edge height adjustment). For example, if a 1/2" ROH shows 0.002" of edge height misalignment (1 line up on the right side of the edge checker and 1 line down on the left) this requires the user to adjust the Sparx by turning the adjustment knob between 5 and 6 "clicks" - or moving the grinding wheel in or out by 0.008". This amount of accuracy in Grinding Ring movement is really impressive when you consider the alternative which is an iterative trail and error approach to alignment (like you get with traditional manual sharpening equipment). The comment "Any experienced sharpener knows that CCM blades are wider than Bauer blades" is just plain inaccurate. As I write this I am holding a Bauer LS2 and a CCM SB Stainless blade in my hands. I am measuring their thickness on a Fowler Micrometer with a reading out to 5 decimal points. The thickness of these two pieces of steel is statistically identical (0.1140"). Saying that CCM is wider is wrong and could be misleading to readers of this forum. What is true is that all steel varies in its thickness. This is especially true of Black Steel and Chromed Steel and the like. We will soon be posting the results of a study we're doing on steel thickness and this data is going to surprise a lot of folks. Stay tuned to our Facebook page or our website for that post soon. The beauty of Sparx, and one of the main motivations for starting Sparx, was to build a product that doesn't care about the variations in steel thickness. This variation is what makes manually sharpening skates so difficult and time consuming and full of opportunity for people to make mistakes or be lazy. The centering skate clamp of Sparx, which is the exact same clamp design and hardware for both our consumer and pro machines, puts the blade over the center of the grinding wheel every time. SG: Ease of use (10/10) - could train staff to use this thing in 5 min. Very easy and simple to use. Any player over age 10 could handle it safely. Sparx: Thank you. We had ease of use as one of our most important design criteria when building Sparx. SG: Speed (7/10) - I can sharpen a pair of skates faster, and I really take my time to make sure they are perfect. Advantage is you can set it and leave and work on other things. About 7 min a pair with changing the skates out. Sparx: This one really depends on the user and the type of install. Take the home user. I am an adult league hockey player and I have a first year bantam player at home. Both of us sharpen every time we skate and we use 2 cycles per skate. A cycle on Sparx is about 45 seconds. This means I spend a bit over 3 minutes each time I play to prep my or my son's skates. This is about the time it takes me to put my gear in my hockey bag so I get both done at the same time. Now consider the pro user. New England Sports Center, an 8 rink facility in Massachusetts, has four Sparx Pro Sharpeners. With these sharpeners, they can sharpen 2 pairs of skates in under 4 minutes. All this while keeping the quality and consistency of the sharpening very high with any employee. This is a major win for their retail operation. Depending on the store size and volume, a Sparx commercial user will choose the number of machines that best serves their operation. For any retailer, losing even a small fraction of business on account of super long sharpening queues or inconsistent sharpening results is a terrible thing. Sparx makes running a commercial sharpening operation more streamlined. SG: Quality of equipment (4/10) - it is a heavy-ish unit, however heavy does not mean quality materials and construction. For a commercial piece of equipment, it looks and feels more like a toaster oven. The vacuum (that you must buy or they void your warranty) is a bucket mount POS that you can buy at home depot. They do include a hepa filter that is just a piece of foam (we are sucking up metal - the only thing needed is something that does not allow the metal particles to go in or near the motor). The motor is bigger than the one that comes with the home unit, and they say it is good for 3200 pairs a year. I dont believe that for a second, however I have no evidence or facts to support my statement. The edge checker is crap. The lines are very far apart, and the general construction is not good. The stone is also crap, but not really a big deal for a pro shop as we have plenty of high quality stones. Sparx: All things equal, heavy is typically a good thing when trying to reduce vibration in a piece of equipment. Look at any milling machine and you'll notice the cast iron base that it is sitting on. There are far lighter ways to construct a base but this help minimize vibration in the mill. SG is right that this doesn't automatically mean quality though. The main component in the Sparx chassis is an incredibly beefy and stiff extrusion. The rest of the chassis is a thick steel enclosure. This is where most of Sparx's weight comes from. The plastic components that dress-up the Sparx unit are just covers... similar to the way automobile companies trim the steel and aluminum structure of the car with plastic bumpers and ground effects for aesthetics. We wanted to make a skate sharpener that not only sharpened well but also looked beautiful so people would be proud to show their friends. The motors used in the commercial Sparx were tested to tens of thousands of sharpenings in our lab before they were ever released to customers. We plan to do a YouTube video soon that highlights our R&D labs and test chambers. We have a chamber where we can run 24 Sparx Sharpeners 24 hours a day 7 days a week. These ran continuously for months before we released the Sparx Pro machine this past summer. The sound of 24 Sparx machines running simultaneously was really awesome. If you consider Sparx vs our closest competitors, we stand behind our machines by NOT having a cycle limit on our commercial product warranty. Other machines limit their warranty to a cycle limit. SG commented "The edge checker is crap". We disagree and believe our edge checker is actually the most accurate on the market. Our measurement lines provide the same 0.001" edge height resolution that the other edge checkers have on the market. Our measurement lines are machined into the edge checker in the same machining setup as the blade slot which ensures that the relationship between the blade and the lines is the most precise that it can be. We also have a few features on our edge checker to preserve the integrity of the measurement lines and the measurement bar so that use doesn't cause the accuracy of the edge checker to deteriorate. Not so on competing edge checkers. We also QC every edge checker before it goes out with a "gold standard" blade to make sure it reads accurately. There are some nuances to blade thickness and taper which can throw off any edge checker - and we'll be putting out a post based on our research in this area very soon. SG: Quality of sharpening (3/10) – we tested many pairs of skates and had two of them tested on the ice. After much fine tuning and adjusting, we could not get a single pair to come out with level edges at both ends of the skate. Not out by much, but out enough that I would never let them leave my shop that way. Part of the issue is the click adjustment setting, and the other is that I think the rail the motor and disk runs on was not straight. Not out a lot, but enough that skates were not level at both ends. You could get one end level but not the other. Click it one adjustment the other way, and it would do the exact same thing the other way (vice versa). One pair tested on the ice was by a coach and he said they were fine and felt no difference. The other was tested by a Bantam player, and he knew right away that the edges were out. The disk leaves a very heavy burr (compared to a standard sharpening wheel) along the entire edge of both sides of the blade. This can be removed with a course stone with extra passes. With standard sharpening a fine hone works great. The hollow itself does have a little bit of chatter. Probably about the same as traditional sharpening. However, if you make a slower last pass and / or use finishing oil or wax, traditional sharpening has a far superior blade finish. This was a brand new in the box demo unit (we were the first test). Maybe this was a bad one, or maybe this is normal for the Sparx. Either way the quality was not good enough for me to actually send a pair back out over the counter to a paying customer. Sparx: There is a lot of stuff to comment on here. First, there are NHL teams putting players on the ice in NHL games with Sparx. These pro hockey players have the 10,000 hours of skating experience to make them the best in the world. SG is telling us a couple funny things here. The first, "I would never let them leave my shop that way" is just totally false. We have visited dozens and dozens of shops and heard this exact same claim. When we then go and randomly grab a pair of skates from a shop's finished sharpening pile they almost always have some amount of uneven edges. Then comes the excuses about why this pair or that pair... come on. Respectfully, the same goes for NHL guys sharpening. When someone says they never let a pair go out that aren't perfectly level don't listen to them. Skates are perfectly level when within 0.001" of perfectly level. Trying to get them more level makes no sense. The accuracy of every part in the tolerance stack to make the edge height measurement exceeds the accuracy of the exactness you're going for. This is engineering 101. Blade thickness taper alone is such a major factor in this edge height measurement. The second comment that needs to be addressed is "One pair tested on the ice was by a coach and he said they were fine and felt no difference. The other was tested by a Bantam player, and he knew right away that the edges were out." Really? So NHL players can't tell, the coach you sharpened for can't tell, but this 13-14 year old Bantam player is proof positive that Sparx is inaccurate. Hmmmm. Seems like we might be jumping to a conclusion from a very small sample set. The comment about a Sparx leaving a burr that is bigger than a traditional vitrified bonded wheel is something we can't argue. I would have to say on average, I do wind up working out more burrs with Sparx than I do with a traditional wheel. The reason is for this highlights a few aspects of a traditional sharpening wheel that could be problematic. The bonded wheel of a manual sharpener is consumed by the skate blade during the sharpening (put your hand in the swarf of a traditional sharpener and you'll feel the wheel dust flying off the wheel as it sharpens) and the blade itself digs into the wheel and the burrs are taken off by the wheel. This means two things that might not be good... even though there is less of a burr. The first is that the ROH on a bonded wheel is constantly changing. When dressed to a 1/2" ROH, a bonded wheel holds that ROH accurately for a couple rotations of the wheel hitting the skate steel. The ROH is then getting altered in the process of sharpening. This means inconsistent ROH from pass to pass and skate to skate. The Sparx grinding rings are precision machined steel substrates with a single layer of superabrasive coated onto them. The ROH doesn't change from the 1st pass to the last pass on a Sparx Grinding Ring. The second is that the edges are being dulled by the traditional grinding wheel as it wraps around the steel as it wears and removes the burr in the process. With Sparx you do need to, on occasion, put a few more seconds into deburring but this isn't a big deal and we suspect in the end the burrs are equally removed from both sharpening types. SG: Cost of unit (4/10) – cost of the commercial unit including vacuum, edge checker, pick guard, all 3 blade holders for loose steel, and a 3 pack of stones is $3244 CDN. If you run a busy pro will need all of those things. One scary thing is they do sell a 2 year and 3 year add on warranty? Sparx: Our costs are shown on our commercial website here. https://www.sparxhockey.com/pages/commercial-homepage I wish we could do something about the USD/CAD exchange rate but that is beyond our control at Sparx. We sell the add on service plans in the same manner that nearly all products do. The sharpener is warranted, as I mentioned above, for unlimited cycles in the base time period. If you want to add calendar years to this coverage this is an additional charge for peace of mind for a business that desires it. Many of our commercial customer love Sparx for all of the labor flexibility benefits and the ability to sharpen many more pairs of skates with fewer resources. These customers often want to buy additional insurance so that,if they ever have a problem with their Sparx machine in years down the road, we will support them in a white-glove fashion. These extended service plans provide that insurance and peace of mind. Again, this is a very common practice with durable goods such as our product. SG: Practicality for a pro shop (5/10) – It has some good points and some bad. Good is ease of use and training staff. Bad is quality of sharpening and cost of each sharpening. As a back-up machine to a regular sharpener it might have some value if it produced quality sharpenings. As a stand-alone machine in a pro shop no chance. There are too many variables it can not accommodate for. Bent blades, differing thickness of blades, nicks, gouges, changes in hollows, bent holders, loose blades, etc. For home use on 1 to 5 pairs of skates all at the same hollow it would probably be ok. Sparx: We already have 100's of commercial users. NESC here in MA sharpens more than 10 times as many skates as SG does per year and they use Sparx as their primary equipment. Hard to argue with that. Bent blades should either be straightened or replaced... independent of sharpening equipment. Different thickness is accomodated for by the Sparx centering clamp. Nick, gouges - easy to address with Sparx. The commercial Sparx machine also has cross grinding (possible on the commercial machine due to the external vacuum). Changes in hollows - easy with Sparx. We have 24 ROH types including flat bottom profiles. Bent holders, loose blades - should be fixed... independent of sharpening equipment. All of the arguments put forth here do not provide any basis on which to reject Sparx as a skate sharpening machine option for anybody - proshop or home user. I hope this helps anyone considering Sparx for Home or Commercial Use. Please reach out to us at help@sparxhockey.com if you have any more questions. Cheers, Russ -
Sparx Skate Sharpener - At home sharpener
ZamboniFever replied to tamtamg's topic in Ice Hockey Equipment
Hi All - Russ here We sent out a note last night to all Sparx customers regarding the X-Grind ring. Bottom line - follow the updated Maintenance Instructions in the Maintenance section of the Sparx Operating Manual. Here's also a link to a similar conversation on our forum regarding the X-Grind Ring (includes a link to the email we sent last night if you didn't get it). https://www.sparxhockey.com/pages/sparx-sharpening-forum#!/general:cross-cut-wheel Regards, Russ -
Sparx Skate Sharpener - At home sharpener
ZamboniFever replied to tamtamg's topic in Ice Hockey Equipment
Thanks for the excellent question mc88. Great job figuring out the workaround for skates that have an unevenly worn heel/toe. This is a technique that our commercial users employ all the time for skates blades like the ones you described. One of our team members here at Sparx created a video to explain this modified sharpening process. There's also a tweak to your workaround to get the last 2-3% that you're missing. I hope this helps... Just as an FYI - There are many cases where I don't feel it's necessary to clean up every bit of previously sharpened blade at the toe/heel, especially if the heel or toe is excessively worn (e.g. banana shaped). What we find is that most professional sharpeners are only trying to reach up there for cosmetic reasons (unfortunately they also are the ones that create this excessively worn area trying to reach up there). If you're positive that you'll never be skating up on this 2-3% of edge - there's a good chance you don't really need to sharpen it AND you'll just be wasting your time tweaking the skate/machine to get it. The nice thing about Sparx is it's pretty easy to take care of if you want to and also easy to skip... it's your call. Whatever makes you most comfortable on the ice. Best regards, Russ -
Sparx Skate Sharpener - At home sharpener
ZamboniFever replied to tamtamg's topic in Ice Hockey Equipment
Hey Guys and Gals - Russ here from Sparx. I thought I would check in to MSH tonight to see if anyone had questions about Sparx. I can address some of the wheel life questions raised above and also provide an update on the feedback we are getting. Hopefully you're cool with me chiming in. I figured it's best to hear it from the source. First, on wheel life. Each Sparx grinding ring has a useful life of 40 skate sharpenings (pairs of skates). One sharpening is two skates at 4 cycles (1 cycle = down and back across blade) per skate or 8 cycles total per pair. 8 cycles * 40 pair = 320 cycles per grinding ring. This is how long the abrasive lasts on the ring. The Sparx Sharpener has a "grinding ring life" display on the top of the unit which has 10 segments. Each segment represents 10% of the life of a wheel or 4 pairs of skates to be sharpened. 10 segments * 4 pair per segment = 40 pairs of skates (4 cycles per skate, 8 cycles per pair) Kgbeast asked about blade length - this doesn't play into the life calculation. Each ring sharpens 40 pairs of skates (320 cycles) regardless of skate size. Users can adjust how many cycles will be run on their skates. We set the default to 4 cycles because that's what we found worked best for people skating a few times in between sharpenings. As a side note - Sparx removes the same amount of material per pass that an average human sharpener does (we figured this out experimentally and then designed Sparx to mimic that removal rate). Sparx also provides constant pressure everywhere along the skate blade length so your blade rocker/radius never changes. With Sparx you'll never get the banana effect at the heel and toe. One of the greatest benefits of Sparx is that your sharpening behavior changes from a repair mentality to a preparation mentality. Many people who own Sparx now sharpen their skates every 1 to 2 times they skate. Across my whole playing career I always felt super confident on my skates right after I got my skates sharpened and then my performance and confidence would degrade until I finally broke down and went to get them sharpened again (up and down throughout the whole season). You'll never experience that behavior again once you have Sparx. With Sparx it's so easy to keep your skates in perfect condition at all times and it only takes 3 - 5 minutes to touch up your skates before every game or practice. Once you get in the habit of sharpening more frequently you can experiment by dropping your cycles down to 3 per skate and this will extend the life of your grinding wheel by 25% (or 50 pair of skates per grinding ring). If on the other hand you get a massive ding in your blade you may need to try more cycles to get it out and that will speed up the ring usage. We do sell a cross grinding ring for the deep nicks and dings... check out our site for that. We recommend this for shops or folks that routinely get huge gouges in their blades. Again, once you change your sharpening behavior you'll get these massive dings a lot less often. The other question asked was about changing from one ROH to another or from FIRE to ROH or back. I find that the normal 4 cycles seems to work for me when switching between hollows (e.g. 1/2" to 5/8"). One way to know for sure is to put black marker (I use a sharpie) on the surface of the blade in a few spots and try it for four cycles and confirm that the marker is removed. If the mark is still there, try another cycle or two and you'll be all set. Sparx is super easy to switch between ROH and FIRE (flat bottom) and experiment to find the hollow that suits your playing style best. Almost everyone at Sparx is skating on something different after experimenting with various hollows. This goes to show you that most people, even our in-house Olympian, will find experimenting to be quite valuable. I thought you guys might enjoy an update on Sparx in general. We now have 100's of Sparx machines out in homes, teams, and pro shops in N. America. We have been most surprised by the pro shop adoption. Our commercial users see the operational benefits of Sparx and the value this product brings to their customers by providing them with a consistent sharpening and with quick turn-around. If you're not in the market for Sparx keep your eyes out for a shop near you using Sparx. If you are in the market for your own machine (convenience is king) we're nearly out of backorder. In the next month or so customers will be able to order Sparx and have it ship same day. We are still accepting pre-orders (no charge until we ship) so if you want Sparx for the start of this season you should buy it now as we are getting new pre-orders every day. We also recently met with many NHL/AHL/and college teams at the annual meeting of pro equipment managers in Nashville. At this meeting we were grilled by some of the most particular skate sharpeners in the world and we impressed the heck out of these guys. One such EM from a pacific northwest NHL team spent over an hour interrogating me and the machine. He evaluated surface finish, edge height evenness, edge smoothness, ability to handle bent blades, ease of alignment, and on and on. We survived and he is one of the first NHL EM's that will be trialing Sparx coming up in the next few weeks. In total we have around 2 dozen such trials pending and our fingers are crossed that we'll get the green light for some to use Sparx in the regular season. Here's a link to the talk I gave at the conference for anyone interested in hearing me talk even more about Sparx: https://www.facebook.com/sparxhockey/videos/1053048344780569/ Hopefully these answers and the update helps people out. We are here for you guys anytime you need us at help@sparxhockey.com. Enjoy the rest of your summer, Russ Layton CEO/Founder, Sparx Hockey -
Sparx Skate Sharpener - At home sharpener
ZamboniFever replied to tamtamg's topic in Ice Hockey Equipment
I forgot to mention - when you pre-order a Sparx Sharpener today your CC is not billed until we ship your product to you. -
Sparx Skate Sharpener - At home sharpener
ZamboniFever replied to tamtamg's topic in Ice Hockey Equipment
Hey guys, Russ here from Sparx Hockey. I just saw this thread and wanted to thank you all for the great support and feedback. As a thanks, I'd like to offer a limited $50 off coupon towards a new Sparx sharpener good through this weekend for any mod squad members that use the promo code MSH-SPARX If you have any other questions or thoughts on the product we'd love to hear from you so feel free to leave a message here and I'll do my best to respond or shoot us an email at help@sparxhockey.com Thanks again and good luck this season!