Slate
Blackcurrant
Watermelon
Strawberry
Orange
Banana
Apple
Emerald
Chocolate
Marble
Slate
Blackcurrant
Watermelon
Strawberry
Orange
Banana
Apple
Emerald
Chocolate
Marble
Archived
This topic is now archived and is closed to further replies.
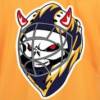
2 piece stick Assembly question
By
Cosmic, in Ice Hockey Equipment